Cos’è il Material Requirements Planning (MRP)?
18 novembre 2024
Metronomo.Net
Il software nato in produzione, per la produzione
L'MRP, acronimo di Material Requirements Planning, è un software fondamentale per la pianificazione della produzione nelle aziende manifatturiere, mirato a garantire un utilizzo efficiente delle risorse disponibili. Il suo obiettivo principale è calcolare con precisione le quantità di materie prime necessarie per soddisfare la domanda di produzione, stabilendo anche il timing per l'approvvigionamento delle stesse. In questo modo, l'MRP consente di evitare carenze che potrebbero rallentare il processo produttivo, così come di prevenire la sovrapproduzione, che può generare eccessi di inventario e sprechi indesiderati.
Attraverso una gestione integrata e un attento monitoraggio dei cicli di lavoro, il sistema MRP coordina meticolosamente ciascuna fase del processo produttivo, partendo dalla gestione delle forniture iniziali fino ad arrivare alla consegna del prodotto finale. Questa coordinazione è fondamentale per garantire che le materie prime siano disponibili al momento giusto, riducendo al minimo i tempi di inattività e ottimizzando l'efficienza operativa complessiva. Inoltre, grazie ai continui sviluppi tecnologici e all'innovazione nella gestione aziendale, l'MRP ha subito una significativa evoluzione nel corso del tempo.
Storia e evoluzione dei sistemi MRP

La storia dei sistemi MRP ha avuto inizio negli anni '60 con l’ingegnere IBM Joseph Orlicky, quando l'MRP emerse come una vera e propria "killer app" per la gestione aziendale, catalizzando l'adozione di software e computer nel mondo dell'industria. In un periodo di boom economico postbellico, l'attrattiva di un sistema in grado di ottimizzare la produzione era altissima: aziende di ogni dimensione si affrettarono a implementare questa tecnologia per migliorare l'efficienza e, di conseguenza, i guadagni. L'MRP consentiva infatti alle imprese di calcolare con precisione il fabbisogno di materiali, aumentando la velocità di produzione, diversificando l'offerta e abbattendo i costi.
Negli anni '80, è stata introdotta un'evoluzione dell'MRP, nota come MRP II (Manufacturing Resource Planning II) che ha ampliato il concetto di pianificazione includendo non solo i fabbisogni di materiali, ma anche altre risorse aziendali come la capacità produttiva, la manodopera, i macchinari e le informazioni finanziarie. Questa metodologia offriva una visione più completa e integrata della gestione della produzione, consentendo una pianificazione e un controllo più efficaci dell'intera catena produttiva, dalla materia prima al prodotto finito.
Con il passare degli anni, in risposta all'evoluzione dei mercati e all'emergere di una concorrenza sempre più agguerrita, i moderni sistemi di pianificazione delle risorse sono diventati notevolmente più sofisticati, integrando funzioni avanzate per la gestione di inventari, supply chain e risposte tempestive a eventi imprevisti. Oggi, le aziende si affidano a questi sistemi avanzati non solo per ottimizzare l'efficienza produttiva, ma anche per affrontare le sfide di un ambiente di mercato in rapido cambiamento, rendendo l'MRP una pietra miliare nel panorama della gestione aziendale contemporanea.
Differenze tra MRP e MRP II
L'MRP e l'MRP II rappresentano due approcci distinti nella pianificazione e gestione della produzione aziendale. Mentre l'MRP si basa principalmente su un piano di produzione predefinito, l'MRP II adotta una visione più ampia, integrando analisi della domanda e del mercato per migliorare la pianificazione. Inoltre, l'MRP tende a fare affidamento sull'esperienza passata dell'azienda per ottimizzare i processi, mentre l'MRP II si focalizza sull'analisi delle performance correnti e sull’utilizzo di dati aggiornati per prendere decisioni più informate.
Un’altra distinzione significativa risiede nel tipo di feedback utilizzato: l'MRP è considerato un sistema aperto, mentre l'MRP II integra dati provenienti da report analitici, permettendo una rielaborazione costante delle informazioni. Infine, sebbene l'MRP si concentri essenzialmente su aspetti legati a quantità e tempistiche di produzione, l'MRP II si occupa anche della pianificazione delle risorse necessarie per attuare i vari processi produttivi, offrendo così una gestione più completa e coordinata delle funzioni aziendali.
Funzionalità chiave dei sistemi MRP
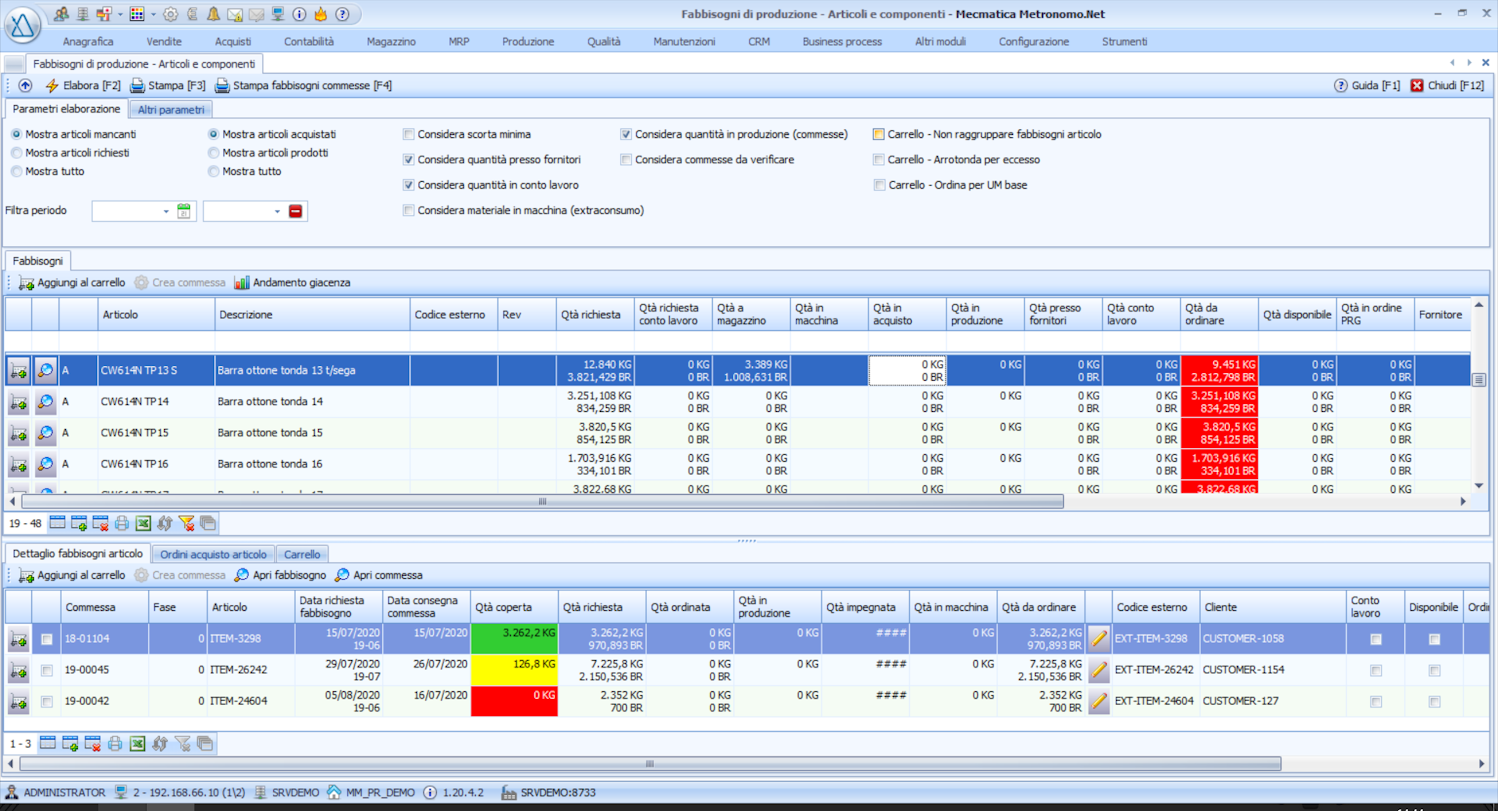
Un sistema MRP moderno rappresenta una soluzione altamente integrata e a circuito chiuso, in grado di gestire le operazioni di un'intera azienda. La sua funzione principale è quella di monitorare costantemente le attività aziendali e di relazionarsi con i sistemi di pianificazione e programmazione per garantire che le promesse fatte ai clienti siano sempre rispettate. Le fasi chiave del processo MRP includono:
Definizione accurata di ciò che deve essere prodotto: la progettazione è responsabile della creazione e gestione della distinta base per i prodotti finali e i sottoassemblaggi. Questa struttura gerarchica delinea in modo preciso il contenuto e la sequenza necessaria per ciascuna unità, specificando quali componenti dipendono da altri e in quale quantità;
Quantificazione della domanda: il sistema calcola quantità e date necessarie per i prodotti finali in base agli ordini dei clienti e alle previsioni di vendita, sottraendo lo stock disponibile. A seconda del modello produttivo adottato, le aziende possono focalizzarsi sugli ordini in arrivo, su previsioni o su una combinazione di entrambi, creando così un programma di produzione principale che allinea le aspettative di tutti gli stakeholder coinvolti;
Definizione della fornitura: grazie alla distinta base e al programma di produzione principale, il modulo MRP determina gli assemblaggi, i componenti e i materiali necessari per il periodo di pianificazione. Verifica poi le quantità richieste rispetto all'inventario disponibile, attraverso un processo noto come netting, per identificare eventuali carenze. Stabilisce quindi la quantità appropriata da produrre o acquistare per ciascun articolo, calcolando le date di inizio per l'acquisizione in base ai tempi di attesa previsti e trasmettendo tali informazioni ai reparti acquisti o produzione.
Vantaggi dell'implementazione di un sistema MRP
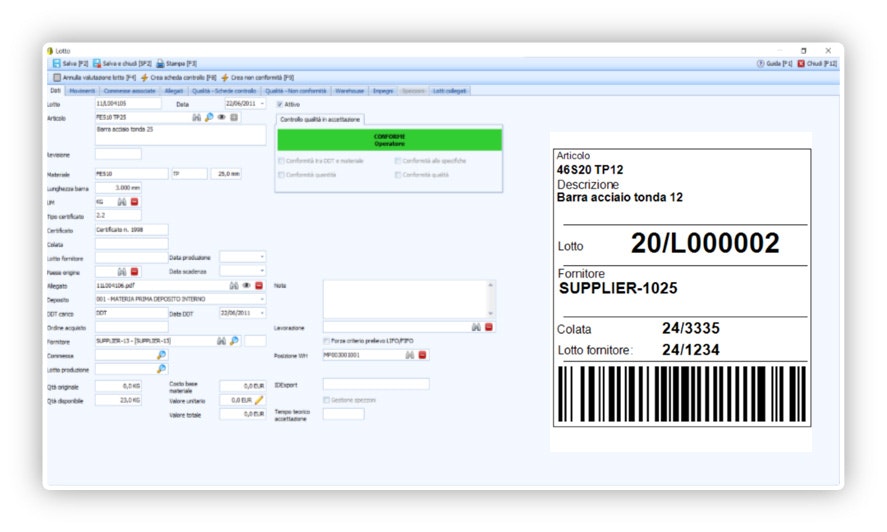
L'implementazione di un sistema MRP offre numerosi vantaggi strategici per le aziende manifatturiere, senza i quali risulta difficile mantenere un buon posizionamento nel mercato. Tra i principali benefici, possiamo elencare:
Ottimizzazione della pianificazione: l'MRP consente una pianificazione più accurata delle risorse materiali e produttive, essenziale per gestire complessità elevate e volumi di produzione significativi;
Gestione efficiente dello stock: grazie a una previsione precisa dei fabbisogni, l'MRP favorisce la gestione ottimale delle scorte, evitando sia eccessi che carenze di materiali, fattori cruciali per contenere i costi e garantire la produttività;
Riduzione dei costi: una gestione più efficace dello stock si traduce in una diminuzione dei costi operativi, poiché la presenza di scorte in eccesso comporta costi di stoccaggio e gestione elevati;
Miglioramento della programmazione: l'MRP supporta la programmazione delle attrezzature e del personale, assicurando che le risorse siano allocate in modo appropriato e tempestivo;
Adattamento al mercato: l'implementazione di un sistema di MRP consente alle aziende di rispondere rapidamente alle variazioni della domanda, migliorando la flessibilità operativa e la capacità di rispondere alle sfide del mercato;
Miglioramento del servizio clienti: una gestione accurata delle scorte e una pianificazione efficiente portano a una maggiore affidabilità nelle consegne, migliorando così la soddisfazione del cliente.
L'importanza del MRP nella supply chain
La supply chain comprende l'intero ciclo industriale, dall'approvvigionamento delle materie prime fino alla consegna del prodotto finito al cliente: una gestione efficace di questo processo è essenziale per mantenere la competitività sul mercato. L'MRP, attraverso una pianificazione precisa e una gestione ottimizzata dell'inventario, consente alle aziende di coordinare in modo efficiente tutti i flussi di materiali e informazioni all'interno della supply chain. Ciò porta a una maggiore reattività alle variazioni della domanda e a una riduzione delle interruzioni nei processi produttivi.
Per le aziende che vogliono implementare un sistema MRP nella supply chain, il primo passo è analizzare i processi produttivi e logistici per capire dove ci sono possibilità di miglioramento. È importante avere chiari gli obiettivi e le risorse necessarie per l’implementazione. Dopo avere installato il software, la formazione del personale è fondamentale, così come integrare il MRP con gli altri sistemi aziendali. È bene inoltre effettuare una fase di test per assicurarsi che funzioni come previsto e si adatti alle specifiche esigenze dell'azienda.
A chi serve un sistema MRP?
Sebbene si possa credere che l'MRP sia una funzionalità esclusivamente riservata alle imprese manifatturiere, è fondamentale riconoscere che il concetto di "azienda manifatturiera" comprende una vasta gamma di attività. In termini di calcolo MRP, un produttore è qualsiasi entità che acquista materiali o componenti e li trasforma in un prodotto finale che può essere venduto ai consumatori:
Magazzini che confezionano articoli o assemblano set di prodotti in “kit” o combinazioni per la rivendita come unità;
Magazzini che creano configurazioni personalizzate dell'ordine, conservando sia le unità principali che i componenti accessori per montare il prodotto personalizzato prima della spedizione;
Fornitori di servizi che assemblano pacchetti di documentazione, strumenti, materiali di consumo o altri beni tangibili destinati a clienti o pazienti;
Gestori di edifici per uffici, ospedali, strutture governative e complessi residenziali, per la gestione di forniture e attrezzature in base all'utilizzo previsto;
Ristoranti che applicano un sistema MRP per controllare le scorte e il approvvigionamento degli ingredienti e dei prodotti.
Integrazione con altri sistemi: MRP, ERP e MES
L'Enterprise Resource Planning (ERP) e l’MRP sono due sistemi di gestione aziendale interconnessi, con l'ERP che può essere considerato un'evoluzione del MRP, integrandone le funzionalità e ampliandole verso nuove aree operazionali. Originariamente, l’MRP si concentrava sulla gestione dei materiali, prevedendo necessità in termini di quantità e tempistiche; con l'introduzione del MRP II, vennero aggiunte funzioni finanziarie e contabili, facendo di questo una base solida per sviluppare l'ERP moderno.
Oggi, l'ERP non solo ingloba le capacità dell'MRP, ma si estende a una vasta gamma di funzionalità che includono la gestione delle risorse umane e la pianificazione della catena di approvvigionamento, collegando e coordinando tutti i reparti aziendali per migliorare il flusso di informazioni e la collaborazione. Inoltre, l’integrazione con altri sistemi, come il Manufacturing Execution System (MES), è fondamentale per ottenere una visione olistica delle operazioni aziendali, dove l'MRP si occupa della pianificazione e gestione dei materiali, mentre il MES monitorizza e gestisce l'esecuzione della produzione in tempo reale, consentendo una gestione efficace e coordinata delle attività aziendali.
Conclusioni
Un'analisi dell'MRP può essere paragonata a un mosaico in continua evoluzione. Nel corso di oltre cinquant'anni di evoluzione, l'MRP ha subìto una notevole metamorfosi: da un sistema di calcolo relativamente semplice si è evoluto in uno strumento complesso e indispensabile per il supporto decisionale. Oggi, esso consente a tutte le organizzazioni di attuare pianificazioni e gestioni non solo efficienti ed efficaci, ma anche reattive, trasformando i singoli componenti in prodotti finalizzati a soddisfare le esigenze dei clienti.
Metronomo.Net